5 Types of Extruder Screens Used for Material Extrusion (With Video)
The proper extrusion of material is a vital element to the production process of countless industries, such as the plastic industry. Filtration operators and quality engineers must coordinate to implement the right extruder screens to eliminate the risk of product failure compromising the company’s reputation among its customer base.
With a handful of extruder screen variants on the market, which one should you implement into your extrusion process?
W.S. Tyler has worked with the woven wire filter cloth needed to construct premium extruder screens for over 140 years and our team of experts is here to help ensure you select the right solution for your needs.
In this article, we will go over the equipment that is used to carry out the extrusion process, the different types of extruder screens that are used to filter out contaminants, and the filter element specifications that have become regarded as the industry standard.
What Equipment Is Used During the Extrusion Process?
Before you can truly understand why there are several types of extruder screens, you must first understand the variety of extrusion machines available and how they work. That said, there are currently 3 types of screen changers that are primarily used throughout the extrusion industry: slide plate changers, hydraulic piston changers, and continuous belt changers.
We will now analyze how each of these pieces of equipment carries out the extrusion process.
1. Slide Plate Changers
Slide plate screen changers utilize a mechanical plate to house the filter medium. With a discontinuous system, a mechanism is used to slide the plate out, exposing the filter and allowing the operator to either scrap the filter clean or replace it with a new one.
The biggest downfall of these systems is that when the operator slides the plate out, the flow of material must stop. When the filter medium is ready for use and the plate is secured in its closed position, production can resume.
On the other hand, a continuous slide plate changer is in constant motion, feeding fresh filter mesh as the operation goes. With these systems, you simply change out the contaminated screens as the plate rotates.
2. Hydraulic Piston Changers
A hydraulic piston screen changer uses a hydraulic system to rotate new extruder screens in place of the screens that have become clogged with contaminants and are unusable. Similar to a slide plate changer, hydraulic piston changers are available in both continuous and discontinuous variants.
Regardless of which hydraulic system you use, there is still some manual work needed. An operator must stand by and replace or clean the soiled extruder screens as the hydraulic system activates, and production continues.
NOTE: While slide plate and piston changers may look different, they just use different forms of motion to reach the same end. Both are available through different manufacturers in continuous and discontinuous models with or without self cleaning. Whichever style you might have, W.S. Tyler can provide replacement screens for your application.
3. Continuous Belt Changers
Continuous belt changers are extruder machines that use rolls of woven wire filter cloth to create a virtually endless production cycle. With no need to constantly replace clogged screens, these systems require the least amount of maintenance.
In fact, other than swapping out new rolls of filter cloth, there is little to no maintenance required by the operator.
It should be noted that, regardless of what equipment you use, contaminated extruder screens add back pressure to the system and increase the melt temperature (due to friction), which can reduce the output of clean material.
What Types of Extruder Screens Are Available?
When it comes to the actual extruder screen being used to filter out contaminants, there are five varieties that have become standardized in the extrusion industry: disk, oval, wrap, candle pack, and belt.
In terms of common use, disk, oval, and wrap extruder screens are the most widely used solutions in the industry.
The key difference between the disk and the oval extruder screens is the shape. That said, oval screens do offer more surface area and can filter nearly double the amount of material as standard disk screens.
Wrap around screens take on a cylindrical form that is completely different from the disk and oval screen. As the filter medium wraps around the entire mechanism, these screens offer a tremendous amount of filtration surface area and filter four times the amount of material that a standard disk screen can.
Candle pack screens are arguably the most unique extruder screens on the market, as they consist of several cylindrical filters bundled together. This allows for the filter to provide a level of material flow that the other options can not.
It should be noted that, while candle pack screens provide the best material flow, they stand as the most expensive option.
Continuous belt screens are simply a roll of filter cloth that, instead of fitting into a distinguished housing unit, are placed into a mechanism that gradually feeds clean filter cloth to the filtration mechanism.
What Filter Element Specifications Work Best?
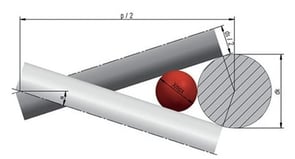
As the solutions listed above have become standardized across the globe, the specifications for the filter cloth have followed suit. This means that no matter which extruder solution best fits your operation, the specification of the filter element will generally be the same.
The diameter size of your screen is dependent on the equipment you use. No matter what equipment you implement in your extrusion process, however, the diameter of your extruder screens will most likely fall within the average diameter range of 30 to 200 millimeters.
With that, extruder screens should have a filter element that ranges from a mesh count of 240 (60 micron) to a mesh count of 180 (1,000 micron).
In terms of the outer supportive layering of the screen, 16 to 20 mesh is commonly used for the back end while 30 to 40 mesh is generally used for the face end.
While single layer screens are the most economical option, higher pressure applications can require facing or backing mesh to protect the filter layer from deformation.
Perfect Your Material Extrusion Process
It is important that filtration operators and quality engineers implement reliable equipment to ensure their material extrusion operation properly decontaminates any raw or recycled material used during production. Failure to do so can result in an inefficient production line or, more importantly, potentially dangerous product failure.
There are 3 types of screen changers that are widely used in the extrusion industry:
- Slide plate changers house the extruder screen in a mechanical plate that is controlled using a level system. As they are discontinuous, these systems require production to halt when changing or cleaning the extruder screen.
- Hydraulic piston changers utilize a hydraulic system to place the extruder screen into place. When more than one piston is used, the flow of material is transferred, allowing for continuous operation.
- Continuous belt changers provide a unique system in that they use a roll of filter cloth, which eliminates the need for the operator to constantly clean or replace the filter medium.
That said, there are five varieties that have become standardized in the extrusion industry:
- Disk and oval screens are typical extruder screens that ultimately differ in shape. Oval screens typically offer more surface area, thus allowing twice as much flow of material.
- Wrap around screens offer similar filtration qualities of disk and oval screens on a much larger scale. As it wraps around the entire filter mechanism, these screens offer up to four times the amount of material flow of disks screens.
- Candle pack screens are composed of several individual filters that are cylindrical in shape. This unique form factor allows for the best flow rate; however, these screens stand as one of the most expensive solutions on the market.
- Continuous belt screens are a roll of filter cloth that is placed into a mechanism that gradually feeds clean filter cloth as opposed to the other options, which require designated filter housing.
Now, as the screens become more widely used on a global scale, the sizes and specifications become more uniform.
In terms of screen diameter, your extruder screens should fall within the average diameter range of 30 to 200 millimeters. a mesh count of 240 (60 micron) to a mesh count of 180 (1,000 micron) should be used for the filtration element while 16 to 20 mesh should be used for the back supportive layer and 30 to 40 mesh for the front supportive layer.
Here at W.S. Tyler, we understand that implementing the right solution is crucial to the success of your material extrusion process. This is why our team of experts takes pride in providing you with the knowledge needed to perfect your operation.
To learn more about the different filter cloth profiles that can be used to create the ideal extruder screens for your process, please download and review our Woven Wire, Fabricated Parts, and Customized Filters Brochure.
You May Also Find the Following Article useful:
About Ronnie Brown
Ronnie is the Content Writer for W.S. Tyler and has four years of experience as a professional writer. He strives to expand his knowledge on all things particle analysis and woven wire mesh to leverage his exceptional writing and graphic design skills, creating a one-of-a-kind experience for customers.