Oil Well Sand Control Screens (Definition, Benefits, and Alternatives)
The oil and gas industry presents some of the most lucrative opportunities; however, many of the mining techniques can negatively affect the quality of the oil. In order to ensure you are producing the best possible product, you must employ a sufficient means of minimizing the amount of impurities that leave the oil reservoir.
This is where sand control comes into play. There are several sand control options to choose from, each designed with a specific application in mind.
That being said, which option is right for your process?
W.S. Tyler has been providing sand control screens for the oil and gas industry for several decades and is here to help you produce the best possible product.
In this article, we will cover everything you need to know about sand control screens, including what sand control is, what a premium sand control screen is, how a sand control screen is formed, as well as the different types of sand control solutions there are.
What Is Sand Control?
In the oil and gas industry, sand control is best described as a method to prevent impurities, such as sand and rocks, from making their way into a wellbore.
So why is sand control so important?
Well, when you initially drill into an oil reservoir, there are several impurities mixed within the oil. If you neglect to implement any sort of sand control, the oil that is obtained will transfer all these impurities to the refining facilities.
Unfortunately, a lot of these refineries do not have the capacity to handle heavy-duty filtration. When unfiltered oil reaches the facility, the impurities may build up within the equipment, which can lead to costly downtime and loss in revenue.
Failure to use sand control can also cause the entire wellbore to get capped. This can be detrimental, as this typically means the company is missing out on millions of dollars.
What Is a Premium Sand Control Screen?
In order to effectively produce quality oil from a wellbore, you must pass the raw oil through some sort of sand control, such as a premium sand control screen.
A premium sand control screen is simply a filter medium that prevents the impurities from leaving the oil reservoir. This filter medium can be anything from woven wire mesh to perforated metal.
How Is a Premium Sand Control Screen Formed?
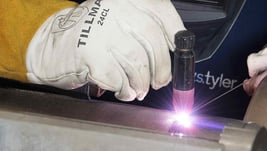
The forming process for a premium sand control screen starts with a diffusion-bonded wire mesh laminate. Each screen consists of a support layer of mesh as well as a filtration layer. The wire mesh laminate is then formed into a tube.
At this point, multiple tubes are welded together at the ends based on the tube length needed. The final step in the process is placing a cap at each end of the single tube.
After the tube is finished, it gets wrapped in bubble wrap, boxed, and shipped.
Read the following article to learn more about how woven wire mesh is welded:
What Is Diffusion Bonding?
Diffusion bonding is the process in which two sheets of mesh are fused on a molecular level.
During the process, one sheet of thicker mesh (for support) is placed on top of a finer sheet of mesh (for filtration). Both sheets are then put into a vacuum and subjected to a tremendous amount of heat.
When the process is complete, the two sheets are not melted together; however, the connection is strong enough for both sheets to be considered one piece.
What Types of Sand Control Screens Are There?
Not every wellbore or oil reservoir is the same. When looking for a sand control screen that will best suit your operation, it is important to know that there are a variety of screens designed for different applications.
Slotted Liner Screen
A slotted liner screen is a tube made up of several pieces of sheet metal welded together. Each piece of sheet metal has a number of straight, slotted holes punched out of them to carry out filtration.
Generally, each of the slotted holes is around 1.5 to 2.5 inches long, with an average width of 0.012 to 0.250 inches.
Now, this is the least expensive sand control option available; however, the low permeability of the tube is a major concern. This means that there is a greater chance of the tube becoming plugged and having a negative impact on the efficiency of the well.
To provide further perspective, slotted liner screens are a great fit for operations that are very budget-conscious or if the oil being extracted from the wellbore is of a higher quality.
Wire Wrapped Screen (Wedge Wire)
A majority of the big-name oil entities use wire-wrapped screens to minimize the impurity levels in their oil.
A wire-wrapped screen is made up of a core tube, which resembles a slotted liner screen, that is wrapped with durable wedge wire to provide a larger flow area. The wire also has accurate keystone slot openings that were designed to decrease the risk of sand plugging.
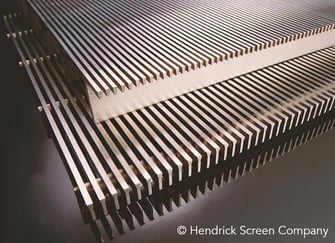
The main issue with wire-wrapped screens is that you can’t go as fine as you can with woven wire mesh. This means a majority of the fine particles will pass through the screen and into the final product.
If filtering finer particles is the desired result, the next two options may be a better fit.
Prepacked Screens
Prepacked screens use an identical keystone slot wire filter seen in the wire-wrapped screens. The main attribute that separates prepacked screens from the other options is the use of gravel between the core tube and wire screen.
This gravel layer serves as a secondary filtration medium that will filter out the finer particles.
When compared to other sand control media designed to eliminate finer particles, prepacked screens are one of the cheaper solutions. This makes it an ideal solution for those looking for an affordable alternative to filter out finer particles when extracting oil from a reservoir.
That being said, the gravel layer raises the concern of plugging. What makes plugging a bigger concern in prepacked screens than the other filtration options is the fact that it cannot be back-flushed.
So, for example, if you were using a slotted liner screen and it became clogged, you could reverse the pressure of the well to push the impurities back into the reservoir. This, in turn, would clear the filter medium and allow the oil to flow through the tube again.
Because the particles causing the blockage become so embedded in the gravel, this process cannot be done with prepacked screens.
Premium Screens (Diffusion-Bonded)
Diffusion-bonded premium screens are a two-part configuration. Each screen consists of a wire mesh layer with some sort of support media bonded on top of it.
The pore size of this particular filtration option ranges from 60 to 300 micron, so this is a great solution for applications that involve very fine particles.
The main advantage of using this filtration option is its plug resistance. If the tubing happens to encounter an accumulation of debris, it can be back-flushed with ease, unlike prepacked screens.
However, the main disadvantage of using a premium screen is that it is the most expensive option.
Pinpoint the Perfect Alloy
Implementing a filtration system that will minimize the impurity levels in your oil will help secure a lucrative stream of revenue. That said, when selecting a sand control solution, it is important to know that there are several options designed for specific applications.
If you’re looking for a budget-friendly option or the oil in your reservoir is of higher quality, the slotted liner screen will fit your operation best.
If you are looking for accuracy and you’re not concerned with filtering out finer particles, a wire-wrapped screen is a great solution.
If you want a solution that is cheap yet accurate enough to filter out fine particles, go with a prepacked screen.
If you are looking for a durable, plug-resistant solution that will filter out even the finest of particles, you may want to consider using a premium sand screen.
Regardless of the solution you choose, you should take the time to investigate what alloy you should use to produce sand control screens that are both durable and effective. With over 150 years of filtration experience, W.S. Tyler is here to share the knowledge within our four walls to simplify this task.
Read the following article to learn more about the alloys available so you can begin designing the perfect sand control screens:
About Ronnie Brown
Ronnie is the Content Writer for W.S. Tyler and has four years of experience as a professional writer. He strives to expand his knowledge on all things particle analysis and woven wire mesh to leverage his exceptional writing and graphic design skills, creating a one-of-a-kind experience for customers.