What Are Laminated Wire Mesh Panels? (Plymesh)
Filtration is a demanding process. It requires high-performance parts that function within ultra-precise parameters.
A high-flow rate is usually the goal for a filtration system; however, sometimes it is important to inhibit flow and spread a gas or liquid over a predetermined area in order to accomplish other needs, such as agitation or aiding the movement of a material in a vessel.
For example, in a silo, granular or powdered products often need to flow from the sides to the bottom. Without an aeration pad, the product can stick against the interior of the silo and never reach its destination for further processing.
Fluid tanks are another common area of concern. An aeration pad allows for the gentle, effective mixing of materials without localized saturation or turbulent behavior.
Poor filtration in the above examples leads to a waste of time and resources for users.
In these cases, media like Plymesh can be utilized to great effect.
What is Plymesh?
Plymesh is a multi-layered, woven wire mesh laminate, most often supplied in panels. It is quite similar in construction to our POROSTAR® product, with individual wire cloths bonded together by a special sintering process. The end product is a porous medium for fluidization and filtration applications.
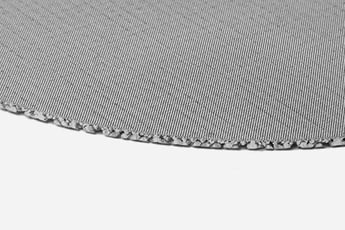
While similar to POROSTAR in construction, the goal of Plymesh is to limit the flow of gas or fluid being passed through the media. These laminated panels can consist of woven wire mesh layers with square openings (plain weave/square mesh), MINIMESH® filter cloth specifications, or a combination of both.
Plymesh owns a defined pore size ranging from five to five hundred microns. The geometry of the pores is uniform, and, unlike powdered metal products, there are no blind holes. The surface of the Plymesh is smooth, with flattened knuckles on the outer wire cloth layers, resulting in something akin to polished sheet metal.
The physical characteristics of the Plymesh, such as pore size and flow capacity, can be predetermined. Because it’s made from stainless steel or other related alloys, the material is temperature and corrosion-resistant. Plymesh can be supplied in panels or ready-for-installation parts, such as candles, cylinders, cones, and aeration pads.
The standard size of a Plymesh sheet is 500 mm x 1000 mm. Special sizes can typically be available upon request.
How does Plymesh work?
Plymesh accomplishes its restricted flow because it is calendered - or flattened - so that its openings become smaller. The heavily calendered layers are then bonded together, creating a tortuous path for the gas or fluid to flow through.
Because of these inhibiting properties, gases or fluids introduced to the media will spread across the surface rather than flow through it, allowing for slow, even disbursement as opposed to outright velocity. The purpose of Plymesh is aeration and fluidization.
How can Plymesh be used?
Plymesh aeration pads can be used to fluidize or optimize the flow rate of powdered and pulverized products in silos and bunkers. Powdered or pulverized goods stored in the silos must be easily extracted for further processing.
The powdered material will often compress or densify during storage and act as if they are a solid. When this happens, it is no longer possible to rely on gravity alone for extraction or movement of the material.
Plymesh aeration pads can be utilized to ensure the ability of the material to flow. These aeration pads and elements are easily installed in silos that are already in operation, making the retrofit cost-effective, especially when considering the efficiency that they would provide for the processing facility.
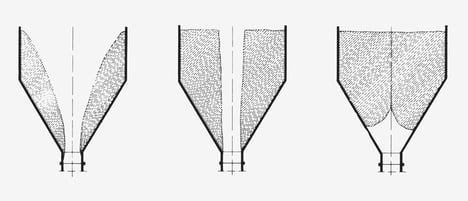
Applications using Plymesh are a highly efficient discharging aid in silos and air-conveying troughs, especially when high temperatures are concerned. Plymesh is a proven separating element in these applications.
Other applications include flow regulator in water pipes, drinking water filtration, sound attenuation for air outlets, filter inserts for air aspirating holes, water separators for fuel, and hydraulic filtration for aviation and aerospace.
What is the typical cost of Plymesh?
Like other wire mesh products, there are a number of factors that determine the final cost.
Basic sheets of material will cost less than a fabricated filter, for example.
When buying sheets of material, you can expect to pay around $125 per square foot. Cost drivers include the following:
The layers of mesh required. Thinner Plymesh, made into simpler parts, will not cost as much as thicker Plymesh, made into more complicated parts.
The amount of calendaring, sintering, and bonding required. These are labor-intensive processes and the price reflects that.
The post-production processing required. After production, the Plymesh may be subjected to further cutting, fabricating, welding, and cleaning.
The fact that the material is often produced in low volumes. Plymesh is made to suit your individual needs.
In the case of Plymesh being fabricated into an aeration/fluidizing pad or similar component, you can expect to pay for the cost of the material plus any additional components and the labor required to produce them.
To explain the cost of Plymesh in a fully fabricated component:
This aeration pad is constructed for continual use in a relatively harsh environment and demands reliable operations.
The different layers of the wire mesh must be bonded together to create the Plymesh, the material must be cut to the desired shape, and the additional components must be precisely welded to the Plymesh. Any finishing, cleaning, and packaging steps then need to be taken into consideration.
In the case of this item, which is around 12” in diameter, you could expect to pay several hundred dollars.
Typically, we aren’t producing these types of items in large scale (100 pieces or less per order), so it must be kept in mind that the fabrication is labor-intensive. While this component is relatively high cost, the value that it offers in an aerating/fluidization application is immense.
To Sum It Up
Plymesh is a laminated wire mesh panel that is ideal for aeration and fluidization purposes. It is durable enough to withstand difficult, harsh conditions, but precise enough to exact the level of material movement required.
By relying on Plymesh, users are protecting themselves against improper filtration practices that cost time and compromise the final product. In silo applications, Plymesh aeration pads facilitate the gentle flow of material from the sides to the bottom for further processing. In liquid applications, Plymesh ensures the gradual introduction of material to a tank, preventing agitated fluid or inadequate mixtures.
W.S. Tyler owns a wealth of experience working with Plymesh, so we can confidently consult on the number and types of aeration pads to deploy in a silo, for example. And retrofitting a structure is more cost-effective than a lifetime of inefficient filtration.
Want all the latest industry trends and innovations sent directly to your inbox? Subscribe to our monthly newsletters today.