How To Clean a Wire Mesh Filter: Understand and Identify the Right Method
In the world of filtration, operation accuracy is of the utmost importance to system operators and engineers, regardless of what's being filtered. This requires best practices to be integrated into the filtration process, especially when cleaning your filter media.
Now, woven wire mesh is proven to be a versatile filter media that delivers a desirable balance of several beneficial qualities. Of these qualities, its cleanability stands out amongst similar options, prolonging its performance.
That said, how exactly do you clean a wire mesh filter?
W.S. Tyler has helped customers understand and utilize the possibilities of woven wire mesh filters for over 150 years and is here to ensure you know how to maintain them properly.
It’s for this reason that the following article will cover:
- What a wire mesh filter is
- The importance of cleaning a wire mesh filter
- The methods used to clean a wire mesh filter
- The cleaning method you should use
What Is a Wire Mesh Filter?
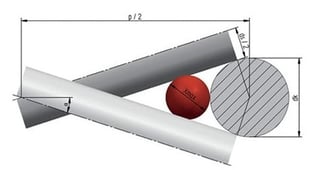
Woven wire mesh is a calculated assortment of metallic wires, typically stainless steel, interlocked together after a centuries-old weaving technique is applied. As this weaving process is monitored closely, high-quality wire mesh features pore openings with the precision and rigidity needed to provide optimal filtration.
To ensure your filtration needs are met, virtually every aspect of the wire mesh weave can be customized. This includes the mesh count, wire diameter, weave pattern, layer configuration, and alloy.
Once woven, the wire mesh is then formed and otherwise fabricated into components designed to fit inside a specific filtration system, screening particles within a designated particle size range.
Why Clean My Wire Mesh Filter?
Regardless of what your filtration process looks like, the effectiveness of your wire mesh filter is the true key to success. That said, obstacles such as blinding, plugging, and overall debris buildup are inevitable.
This is why cleaning your wire mesh filter is essential.
Implementing a regular cleaning routine in your maintenance schedule will keep your wire mesh filter free of any contaminant particle plugging or surface accumulation. In addition, this will ensure your filter system maintains adequate throughput and accuracy for much longer.
Failure to properly clean your wire mesh filter can lead to damaging backpressure, causing your equipment to run less efficiently and increase energy expenses.
Read the following article to learn how you can calculate the pressure drop within your system, providing insight into the efficiency of your operation:
What Methods Are Used To Clean Wire Mesh Filters?
There are currently three predominant cleaning methods you can use to remove residual debris from your wire mesh filter. These methods are backflushing, pressure washing, and chemical cleaning.
Backflushing
The process in which the flow of a substance is reversed within the filter system, purging the filter media of any plugged or accumulated particles in the openings of the mesh. This is an essential step to cleaning a wire mesh filter, as removing the hard-to-reach particles can help ensure you maintain compliant throughput.
Pressure Washing
Pressure washing is the cleaning method that utilizes a pressurized jet of water to remove stubborn particles that can sometimes be difficult to remove. While this method minimizes the amount of manual scrubbing needed, it is not as effective as backflushing when attempting to remove particles that have become plugged in the openings.
Chemical Cleaning
Chemical cleaning is the process in which contaminant particles are removed from the surface of a wire mesh filter using various chemicals, such as detergents, solvents, and alcohol. This process is relatively manual and is the least effective against plugged particles.
What Method Should I Use To Clean My Wire Mesh Filter?
There are several factors that you must take into consideration when determining what cleaning method is suitable for your wire mesh filter. The first thing you should consider is the type of equipment you're using and the installation condition.
To explain this further, let’s say you are using a POROSTAR sintered porous filter. POROSTAR is generally used as filter plates in larger equipment, such as nutsche filter dryers.
These systems aren’t necessarily designed to be backflushed.
That said, because these filter plates are durable and there is room within the equipment, clean-in-place (CIP) techniques are often used. This means that the surfaces that come into contact with the material being filtered can be cleaned using a pressure washing or chemical cleaning method without disassembly.
The alloy of the wire mesh filter itself should also be taken into consideration when selecting the cleaning method. As many wire mesh filters are made from stainless steel, they can withstand all of the cleaning methods listed above.
However, no matter what alloy you use, the cleaning method must align with the durability of the alloy.
Increase Your Filtration Throughput Without Sacrificing Accuracy With Three-Dimensional Wire Mesh
No matter what your filtration process looks like, odds are the effectiveness of your wire mesh is always top of mind. To ensure your wire mesh filters continue to deliver accurate results, it is vital that you properly clean them regularly.
Now, as you continue to fine-tune the accuracy of your operation, you must explore the innovative wire mesh filter solutions on the market, such as three-dimensional wire mesh. This will help you identify whether or not the qualities three-dimensional wire mesh has to offer can be used to improve your filtration capabilities.
With over 150 years of wire mesh filter experience, W.S. Tyler strives to help you make the most out of your filter system.
To get a better idea of how three-dimensional wire mesh can improve your current wire mesh filter, read the following article:
About Ronnie Brown
Ronnie is the Content Writer for W.S. Tyler and has four years of experience as a professional writer. He strives to expand his knowledge on all things particle analysis and woven wire mesh to leverage his exceptional writing and graphic design skills, creating a one-of-a-kind experience for customers.