What To Expect When Designing Screen Printing Mesh
Screen printing is an art that can be traced back to ancient Chinese civilization but holds significant value in today's world. It grants manufacturers and artists alike an avenue to transfer ink to the desired surface, such as solar panels, electronic circuit boards, or glass/porcelain containers.
While more readily available mediums such as silk or nylon were widely used in the earlier years, many screening printing operations have begun to adopt woven wire mesh for its durability and maintainable accuracy. If you are considering switching to woven wire mesh, it's vital that you understand the different levels of customization available to you, as the metallic wires have characteristics that are drastically different from nylon and silk.
At W.S. Tyler, we understand that you ultimately care about one thing about the screening medium: an even distribution of ink. We have worked with hundreds of screen printing processes and have seen it all.
This is why we are confident when we say we can help you capture every detail when screen printing, which will allow you to hit the quality expectations of your customers.
To get you started down a path to success, we will help you learn the ins and out of designing a screen printing mesh. Having said that, this article will cover:
- What screen printing mesh is
- Identifying an ideal mesh count
- The post weaving processes you should consider
- How much screen printing mesh costs
What Is Screen Printing Mesh?
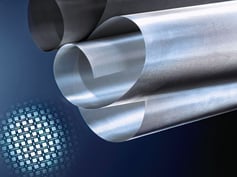
Woven wire mesh consists of hundreds of individual wires that are interlocked together to portray precalculated specifications. This includes the mesh count, wire diameter, cloth thickness.
Screen printing mesh is mesh sheets that is designed to evenly distribute ink during the screen printing process. As woven wire mesh is typically constructed out of stainless steel, it offers a much more durable and precise screen printing medium when compared to other materials such as nylon and silk.
What Mesh Count Should I Use?
When using woven wire screen printing mesh, mesh counts ranging from 25 to 305 are typically used. The mesh count that is right for you is dependent on how much detail the imagery you are trying to transfer as well as the properties of the ink being used.
Having said that, a good rule of thumb to follow is the greater level of detail being transferred, the finer the mesh count will be needed. For example, the highly detailed conductive tracks on a circuit board would require a mesh count of 160 to 200, whereas a t-shirt with large block letters would require a mesh count of 110 and below.
To learn the ins and outs of which mesh count is best for you, read the following article:
What Post-Weaving Processes Should I Consider?
Although woven wire screen printing mesh is generally constructed from stainless steel in an effort to deliver optimal performance, additional value-added services can be applied to ensure your mesh has increased longevity. These services include cleaning, calendering, and cutting.
Cleaning
No matter the mesh specification, it is strongly recommended to have your mesh cleaned after the weaving process. This will help ensure the mesh is free of any residue or debris that could otherwise affect how the ink adheres to the surface it is being applied to.
At W.S. Tyler, we use an ultrasonic cleaning process that employs a specialized cleaning solution and ultrasonic vibrations to remove unwanted debris while remaining eco-friendly.
Calendering
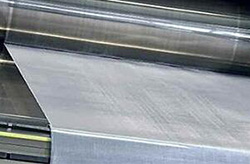
Calendering is a post weaving process that involves wedging the mesh between two steel rollers that applies pressure and heat simultaneously. As a result, the knuckles at each wire cross-section are flattened, and the overall thickness of the mesh is reduced.
When implementing woven wire mesh into your screen printing process, it is recommended that you have your mesh calendered for two significant reasons: to reduce variations in ink deposits with each print and to create a smooth surface that reduces squeegee wear. Now, it's essential to know that there are two types of calendering: Standard calendering and maximum calendering.
Standard Calendering
The standard calendering process takes the mesh and reduces its thickness by 20%, the thickness of double the diameter of a given wire. This process does not affect the accuracy of the mesh opening; however, the surface becomes smooth and shiny.
Maximum Calendering
The maximum calendering process takes the mesh and reduces its thickness by up to 30%, the thickness of double the diameter of a given wire. This particular calendering process allows for the maximum reduction in mesh thickness without altering the mesh's specifications.
Again, the mesh openings are not affected; however, the surface will have a lustrous finish similar to aluminum foil.
Cutting
As the requirements of all screen printing operations are unique, the amount of screening medium needed to transfer the correct imagery is unique to each process. This is why it's important that the screening medium can be customized to fit your operation.
W.S. Tyler has the tooling and experience needed to cut woven wire screen printing mesh to virtually any dimension and specification.
How Much Does Woven Wire Screen Printing Mesh Cost?
There are several factors that can affect the cost of screen printing mesh, including the amount of post weaving services needed, the mesh count, and the quantity of mesh pieces. In other words, the price you can expect to pay ultimately relies on the needs of your process.
Having said that, it is important to note that, because of the amount of labor needed to prep the weaving looms used to produce mesh, the mesh count will be the most significant contributor to cost. This means finer mesh counts require more labor to make, thus cost more than mesh specifications with larger mesh openings.
To that end, screen printing mesh typically has a price range of $3-$15/square foot.
Start Your Woven Wire Screen Printing Mesh Journey Today
Woven wire screen printing mesh are pieces of woven wire mesh that are specifically fabricated to facilitate the even distribution of ink during the screen printing process. While other materials such as nylon or silk were traditionally used, they are known to become bloated and brittle after several uses, reducing their longevity.
This is not the case with woven wire screen printing mesh as the individual wires are metallic.
At this point, you should have an understanding of what screen printing mesh is, the ideal mesh count to use, and what services you should consider applying. To bring this knowledge full circle, the next step is to reach out to our team of experts to sit down and pinpoint the exact mesh specification that is right for you.
From the ink to the screening medium, screen printing is an art that requires material that is reliable and accurate. We strive to become an extension of your team so you can spend less time worrying about the quality of your mesh and more time improving other aspects of your operation.
To being integrating woven wire screen printing mesh and capturing every last detail, contact us using one of the following avenues:
- Go to our Contact Us page and fill out the form
- Email your configuration and contact information to our sales team at info@wstyler.com
- Reach out to us via phone at 800-321-6188
- Provide our interactive chatbot (lower right-hand corner of this page) with your credentials and specific needs
About Ronnie Brown
Ronnie is the Content Writer for W.S. Tyler and has four years of experience as a professional writer. He strives to expand his knowledge on all things particle analysis and woven wire mesh to leverage his exceptional writing and graphic design skills, creating a one-of-a-kind experience for customers.