Design Mesh for Automotive Interior Trim (Uses, Cost, and Challenges)
At W.S.Tyler woven wire mesh is at the center of everything we do. Test Sieves, Screen Printing, Sieve Shakers and Particle Analysis Equipment it all comes back to woven wire.
Normally, woven wire mesh is used for various types of filtration or inside of test sieves. There are hundreds of different opening sizes and weave patterns that offer different levels of filtration and separation.
These patterns also happen to be aesthetically pleasing which makes it perfect as a design element in many industries.
Woven wire mesh fits perfectly into the world of automotive design with its high-end class and customization.
In this article we will dive into how woven wire is used as a design element in the automotive industry. We are going to cover the challenges that come with it, the cost and the different options that are available.
What is Design Mesh?
Design Mesh is a metallic woven wire cloth used primarily for decorative purposes.
We often use our woven mesh in the architectural industry for facades, railing, ceilings and all kinds of interior applications but it has also taken off in the automotive world.
Using Design Mesh can add a new dimension to the product or surface that it is applied to. This material is far less common than painted, solid metallic, or even carbon fiber surfaces.
It is especially suitable for applications where extra texture and light reflection are desired.
How is Design Mesh Made and Used?
Design Mesh is woven on a loom and can be formed into shapes, secured with metallic or plastic-molded framing, laminated with adhesive backing, coated with polyurethane, or wrapped around an existing component.
Depending on the weave used, a certain amount of backlighting or light transmission is possible.
Automotive trim and speaker grilles are some of the best places we have seen design mesh used in this industry.
What Customizations are Available?
Design Mesh is usually made from stainless steel wires, but any type of alloy can be woven to form this material. In addition to stainless steel, options include brass, titanium, aluminum, or copper.
Different alloys can be used in opposing directions to create dramatic effects and patterns.
When it comes to adding color to the mesh, a polyester monofilament fiber (PET) can be used in conjunction with an alloy wire to add a further dimension of color to the material. The PET fiber is available in any color imaginable.
Weaves that use only stainless steel can be annealed or sintered in order to aid in forming and to help prevent the loss of loose wires at the edges.
We have a lot of standard patterns available, but we will also work with you to develop custom patterns depending on your specific design needs.
While we do not convert Design Mesh or produce finished components from it, we can offer suggestions about manufacturing techniques that will help customers attain the end result that they desire.
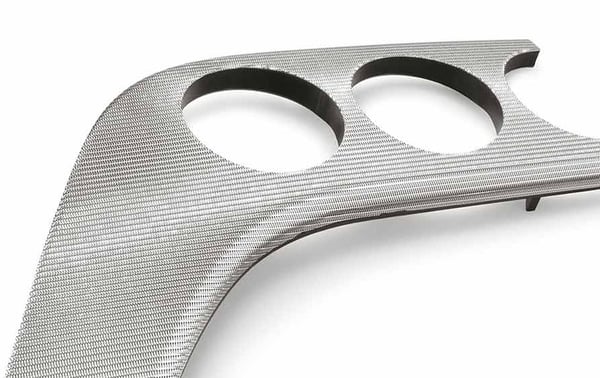
How Much Does Design Mesh Cost?
Like most of our wire products cost is going to vary depending on what type of customizations you might need: weave style, materials used, roll size, backing options, post-processing performed, quantity required.
An average cost to consider is about $8 per square foot but pricing can also be offered per full roll, per square meter, per linear foot, etc.
This material is best suited to applications where a premium or luxury feel is desired. We see a lot of customers choosing design mesh when they are looking for an item that sets them apart from the norm, and when quality & craftsmanship are important.
While material & converting costs may be marginally higher than other alternatives, there is value in the exclusivity and pride of ownership that comes along with a product that incorporates Design Mesh.
What Challenges are There with Design Mesh?
We have added this section to talk about the challenges of using design mesh in your project. We hope that these things help you decide if Design Mesh is the right material for your application, budget, and scope of work.
Converting, Forming and Integration
Design mesh is made of sharp fine wires and some level of expertise is required to mold or form it successfully. We cannot stress enough the importance of picking partners to form or injection mold that have experience with delicate materials like wire mesh.
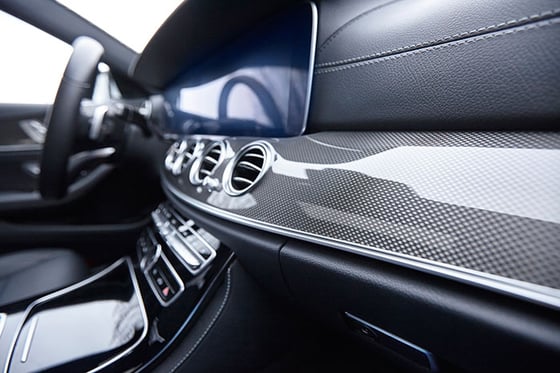
If it isn’t handled correctly it can be very easy to dent, crease or damage. Loose wires along the edges can create possible snags if they are not sealed or hidden properly.
It is extremely important to be careful when cutting to prevent edge fraying - parts are usually laser-cut or cut by water jet.
Injection molding is a great option for around the outside of the component. This helps the material hold its intended shape while also encapsulating the edge to prevent fraying and increase durability.
If forming is involved, the material may resist the required bending.
Forming techniques and converting equipment must be up to par to see the best results.
The fact that woven wire mesh is made up of many openings needs to be considered if you are going to glue or if the substrate is a color that could show through some of the more open weaves. An appropriate backing material must be chosen to prevent this bleed-through of adhesive and to reduce transparency against a mounting surface.
Durability
The delicate nature of Design Mesh can lead to handling damage if it is not prepared or protected correctly.
It is not an incredibly durable material on its own but it can be resilient and long-lasting when used in the correct application and prepared in the right way.
Some ways to ensure that you get the most out of your Design Mesh:
- Location in low-traffic areas- Support with durable substrates
- Encapsulation in polyurethane
- Coating with protective clear-coat
To Sum It Up
The important thing to remember about design mesh is that the customizations are endless. There are truly so many amazing things you can do with color and weave patterns to add a unique and high-end element to any project.
Design mesh fits seamlessly into the fast-paced and ever-changing world of the automotive industry.
We hope this article helped you decide if this might be something that may fit your project or designs and also help you determine if the challenges and costs fit your scope.
If you have any questions about design mesh and how it can work for you, please send us a message and we'd be happy to discuss it with you.