Expanded Wire Mesh vs. Wire Mesh Filters: Picking the Best Filter
From filtering contaminants from gas to extracting a filter cake from a liquid, filtration is a process that relies on accuracy. This leaves filter system optimization as a top priority for filter system operators and engineers.
One of the first steps to improving the efficiency of a filter system is employing a reliable filter medium. This requires operators and engineers to experiment with different materials, such as woven wire mesh and expanded wire mesh.
But what’s the difference between wire mesh filters and expanded wire mesh filters?
Specializing in wire mesh filters for over 140 years, W.S. Tyler strives to help you navigate the various filter media available to achieve the best possible filtration results.
It’s for this reason that this article will cover:
- What a mesh filter is
- The benefits of mesh filters
- The drawbacks of mesh filters
- What expanded wire mesh is
- The benefits of expanded wire mesh
- The drawbacks of expanded wire mesh
What Is a Mesh Filter?
Filter cloth, also known as metal mesh filters, is defined as a network of individual metallic wires interlocked together after undergoing a centuries-old weaving technique that resembles the weaving process used for various fabrics. As a mesh filter is designed to deliver desirable filtration capabilities to virtually any process, all parameters, including the mesh count, wire diameter, weave pattern, layer configuration, and alloy, are customizable.
That said, to ensure the mesh filter fits your system, the mesh supplier can take this customization a step further and leverage the pliable characteristics to form the mesh to fit most filter media housing.
How Is a Mesh Filter Fabricated?
Wire mesh filter cloth starts as hundreds to thousands of individual metallic wire. A weaving loom, specifically designed to handle these metallic wires, is used to properly weave the metal mesh.
These weaving looms are typically made up of a warp beam, heddle frames (predetermined amount), a rapier band, a reed, and a front take-up mechanism.
Now, the weavings process begins with loom operators attaching the individual wires to the warp beam, reflecting the order in which they will be positioned throughout the mesh. The wires are then wound around the warp beam.
At this point, the loom operators thread each wire from the warp beam through the heddle frames and finally through the reed. Once complete, the whole assembly is transported to the weaving hall, and the rest of the loom is attached.
NOTE: As the accuracy of this threading process dictates how precise the pore openings of the mesh filter are, attention to detail is critical.
The weaving loom is now ready to weave filter cloth, and the process begins.
As the weaving loom starts, the warp beam feeds a small increment of wires through the several components while the front take-up mechanism collects and rewinds the same small increment of fully woven wire. These collaborative movements also work to keep the wires drum-tight and properly interlock the wires.
As the warp beam and front take-up mechanism work together, the heddle frames separate the wires. In the first movement cycle, heddle frame one pulls the first set of wires up while heddle frame two simultaneously drives the second set of wires down.
The rapier band then drives a single weft wire in between the separated sets of warp wires horizontally. This weft wire is fed via a separate spool of wire placed or attached on the side of the loom.
As soon as the weft wire is shot across the width of the filter cloth, the rapier band returns to its original position to collect another weft, and the reed pushes the weft forward to its final position. This is what creates the pore openings that deliver accurate filtration capabilities.
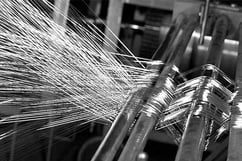
At this point, the reed snaps back to its original position, completing the first movement cycle.
The warp beam and front take-up mechanism then make the same small rotation increment that initiated the weaving process to start a new cycle. As the heddle frames switch position, with heddle frame one driving the first set of wires down and heddle frame two lifting the second set of wires up, the first weft wire that was driven access the mesh sheet is locked into place.
This action is repeated hundreds to thousands of times, depending on the specifications of the filter cloth being woven.
For more insight into how woven wire mesh filters are woven, refer to the article “How Is Woven Wire Mesh Made? (Terminology, Preparation, and Process)”.
What Are the Benefits Associated With Mesh Filters?
As the wire diameter of the wires used to construct a mesh filter can be customized, and the weaving process is heavily regulated, wire mesh filter can be fabricated with pore openings much finer than what is possible with expanded wire mesh. In fact, a mesh filter can have a pore size from 4” to 20 microns (635 mesh).
To that end, mesh suppliers can use several weaving techniques to weave mesh into several weave pattern profiles. As each weave pattern delivers its own set of beneficial qualities, this helps ensure your mesh filter delivers the right filtration capabilities your operation calls for.
What Are the Drawbacks Associated With Mesh Filters?
The most significant difference between a mesh filter and expanded wire mesh is that mesh filters are generally more delicate. This is particularly true as the wire diameter and mesh count of the filter get finer.
Additionally, as woven wire mesh depends on the overall weave to maintain the properties of the mesh, the pore openings are more likely to become skewed. Once a certain number of openings fall out of spec as identified in your industry standards, the mesh filter will need to be replaced as it will no longer have the ability to deliver the required filtration results.
What Is Expanded Wire Mesh?
Expanded wire mesh is most commonly defined as a sheet of metal that is slotted, compressed, and stretched to form a predetermined number of diamond-shaped openings. The durable properties of expanded wire mesh allow it to be used for various applications such as flame arrestors and supportive filtration layers.
How Is Expanded Wire Mesh Fabricated?
When it comes to the production of expanded metal mesh, you must first understand there are two different types of expanded mesh: standard expanded mesh and flattened expanded mesh. Each variant has its own fabrication process.
Standard Expanded Wire Mesh
When producing standard expanded wire mesh, the thickness of the sheet metal used to form the mesh muse first be calculated. This works to ensure there is enough material to expand.
The solid sheet is then run through an expanding machine. As it travels through the machine, a blade methodically cuts slots into the sheet while the machine pulls on the sheet simultaneously.
This expands the sheet metal, creating diamond-shaped openings. The expanded wire mesh sheets are then prepped for shipment.
Flattened Expanded Wire Mesh
The fabrication process used to make flattened expanded wire mesh is identical to the standard expanded wire mesh process. The biggest difference is that, when the openings have been expanded, the mesh sheet undergoes an additional cold rolling process.
This not only flattens and further expands the mesh sheet, but it helps to create a smoother surface.
What Are the Benefits of Expanded Wire Mesh?
As expanded wire mesh starts as solid sheet metal, its durability surpasses woven wire mesh filters. This makes them the ideal solution when filtering large, coarse material, especially when fine pore openings are not required.
What Are the Drawbacks of Expanded Wire Mesh?
The most significant drawback to using expanded wire mesh compared to woven wire mesh is that expanded wire mesh is far heavier of a material. This means your filter system may be subjected to more stress than if a woven wire mesh filter was used.
As a result, your filter system is subjected to a heightened level of stress which can cause costly downtime.
Additionally, while most expanding machines have been automated, expanded wire mesh openings lack the accuracy of woven wire mesh filters. This is because several standards are put in place to regulate wire mesh production as it is widely used for heavily regulated applications.
Achieve Optimal Filtration With the Best Alloy
Fine-tuning the filter system to deliver desirable filtration performance is one of the most significant concerns filtration system operators, and engineers have. The best way to overcome this obstacle is by pinpointing and employing reliable filter media, such as wire mesh filters and expanded wire mesh.
That said, one central element to identifying a filter media that is suitable for your operation is determining which alloy your filter should be constructed out of. This helps ensure that the filter provides the durability to withstand the particles being filtered and deliver maximum efficiency.
Having been a prominent filer mesh supplier for over 140 years, W.S. Tyler is here to provide insight into how the various alloys used to construct filter media perform in different situations.
For more information on what alloy you should construct your filters out of, read the following article:
About Ronnie Brown
Ronnie is the Content Writer for W.S. Tyler and has four years of experience as a professional writer. He strives to expand his knowledge on all things particle analysis and woven wire mesh to leverage his exceptional writing and graphic design skills, creating a one-of-a-kind experience for customers.