How Are Custom Wire Mesh Components Formed?
Woven wire mesh is one of the most versatile solutions in the world of filtration, as it can be formed to fit most operations. While there are other filtration solutions out there, such as perforated plate or wedge wire, formed wire mesh provides a level of efficiency that is simply unmatched.
That said, how exactly are customized mesh components formed?
W.S. Tyler has worked with woven wire mesh for over 150 years and is equipped with the tools and know-how needed to produce formed mesh solutions that are customized to the needs of the customer.
With that, this article was written to provide insight into what formed mesh is, the process needed to form mesh, the common mistake you should look out for, how it’s used, and the limitations surrounding it.
What Does It Mean to Form Wire Mesh?
When you hear the term formed wire mesh, it is referring to the process of taking a sheet or roll of woven wire mesh and converting it into some sort of part or fabrication that maintains a specific shape. These shapes can be virtually anything; it just depends on the needs of your operation.
What Does the Forming Process Look Like?
To form woven wire mesh, we first start with a sheet or roll of woven wire mesh that matches the wire diameter, mesh count, and micron rating specified by the customer. In order for the mesh to maintain the desired shape, the mesh is typically heat-treated through either an annealing or sintering process before being formed.
Read the following article to learn more about how annealing and sintering compare, giving you a better idea of which heat treatment process you should apply:
The mesh is then cut into more manageable sizes then formed using a tooling method, a punch and die, or press brake.
The actual process of forming mesh is fairly quick. In fact, hundreds or even thousands of parts can be formed in as little as an hour, depending on the techniques being used.
To that end, production time can range anywhere from one to four weeks, depending on a handful of factors, such as the availability of material, the details needed to form the part, the quantity of your order, etc.
What Are Some Common Mistakes Associated with Forming Mesh?
As most forming methods are one and the same, there are a handful of things customers should keep an eye out for when working with formed mesh.
For example, it is widely known that while the annealing and sintering processes are crucial, they are accompanied with add-on costs that manufacturers may try to avoid. If these heat treatment methods are omitted from the forming process, the finalized formed piece will be significantly less effective.
If you notice that your formed mesh does not hold the desired shape, this is a key indicator that it was not heat treated properly or at all. This needs to be addressed immediately as the mesh will not function properly, which will have a noticeable impact on your operation.
On the other hand, there are instances in which manufacturers try to compensate for the material’s nature to flex back to its original form by overworking the material. This is done in hopes that the material will spring back not to its original form, but to the desired shape.
Unfortunately, this does more harm than good in most cases. In fact, over-forming mesh often deforms it in a way that renders the part unusable. Even if the piece can be salvaged, odds are the lifespan of the piece will be shorter than expected.
So, if you notice that wires are damaged in any way along the seams or creases of the formed mesh, there is a good chance that the manufacturer over-formed the mesh and damaged it.
What Limitations Does Formed Mesh Have? What Can’t Be Done?
As stated above, mesh can be formed into virtually any shape to help facilitate your operation. As good as this sounds, forming mesh does not come without its limitations.
For example, when forming deep drawn parts, a flat sheet of mesh is drawn to take on a bowl-like form. During this forming process, it is important that we pay attention to how deep we draw the mesh, as there is a ratio based on the diameter of the part that dictates how deep the part can be drawn.
This ratio prevents the depth from having a larger measurement than the diameter of the part.
So, let’s say you have a part that is one inch in diameter. That part cannot be drawn out five inches deep, as there is simply not enough material to form that cavity.
On the other hand, a part that is four inches in diameter can be drawn to a depth of one inch with ease.
How Is Formed Wire Mesh Used?
Formed woven wire mesh is typically used as a filtration medium.
A great example of formed mesh being used in a filtration-based application can be seen in the auto industry. Many automotive manufacturers use formed mesh in the oil pick-up tubes in car engines.
These pick-up tubes are key to the functionality of the car, as they are designed to feed oil from the oil pan to the engine. While this is a very important function, it is also important that no debris or impurities in the oil enter the engine and damage it.
This is where the formed mesh comes into scope.
Manufacturers attach a formed mesh screen at the ends of these pick-up tubes to filter out all the dirt and impurities that make their way into the oil pan over time.
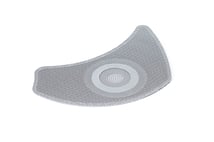
Now, formed mesh can also be seen in our extruder screens and premium sand control screens; however, the list of applications that can benefit from formed mesh goes on and on.
For a more in-depth overview of what can be achieved with formed woven wire mesh, read the article below:
Expand Your Knowledge on Formed Mesh
Formed wire mesh components are pieces or rolls that are fabricated until a desired shape or profile is achieved. They are often applied as a filter medium; however, they can benefit a virtually endless list of applications.
Now, while heat treatment is used to facilitate the forming process, certain formed components must be welded. The welding technique that is applied to your next formed component must be planned out to maintain the accuracy of the mesh.
Having been in the wire mesh business for over 150 years, W.S. Tyler is here to educate you on what is needed to innovate the way you do things through the capabilities of woven wire mesh.
To gain a better understanding of what welding technique(s) should be applied to your woven wire mesh components, read the following article:
About Ronnie Brown
Ronnie is the Content Writer for W.S. Tyler and has four years of experience as a professional writer. He strives to expand his knowledge on all things particle analysis and woven wire mesh to leverage his exceptional writing and graphic design skills, creating a one-of-a-kind experience for customers.