Annealed vs Sintered Wire Mesh: Which Is Best for Me?
From molded pulp to automotive transmission systems, woven wire mesh produces exceptional results in countless industries. In fact, the capabilities of wire mesh are virtually endless when annealed or sintered.
Now, you may be curious as to how the annealing and sintering processes differ and which one is right for you.
With over 150 years of experience working with woven wire mesh, W.S. Tyler takes pride in having the know-how needed to help you make the best decision for your particular needs.
That said, this article will dissect the differences between the annealing and sintering methods, how each process is executed, and the situations in which you may want to apply one over the other.
Why Heat Treat Woven Wire Mesh?
When wire mesh is initially woven, it does not go through any form of heat treatment. This is because there are dozens of applications that call for non-treated mesh.
At the same time, several applications require wire mesh to be formed into a particular shape in order to perform a specific task.
By nature, the wires that make up the mesh weave want to retain their original, straight profile. To ensure the weave retains a desired shape or form, heat treatment is required.
If you attempt to implement formed mesh that has not been annealed or sintered, you run the risk of producing inaccurate results. This is where annealing and sintering come into play.
What Is Annealing?
Annealing is the heat treatment process designed to make the wires in the weave softer and more malleable. During this process, the roll of mesh is exposed to tremendous heat (while staying well below its melting point) and pressure.
Annealing wire mesh reduces the internal stress and hardness of the wires, making the weave easier to form.
What Is Sintering?
Sintering takes the annealing process a step further. When sintering, the mesh is heated to just below its melting point while being subjected to tremendous pressure.
This bonds the individual wires within the mesh at each intersection, preserving the pore size of the mesh.
What Does the Sintering and Annealing Process Look Like?
It’s important to understand that annealed and sintered wire mesh can be fabricated using one of two methods: batch or continuous treatment.
Batch Treatment Process
During the batch treatment process, one or more rolls of woven wire are loaded into a furnace. As it provides the best quantity capabilities but is less controllable, the batch process will work best if you’re working with a coarser mesh or you need a full roll width of 48”-60”.
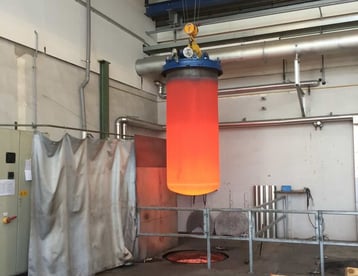
Continuous Treatment Process
The continuous process provides the operator with more control. During this treatment method, a single roll of woven wire is unrolled, run through the furnace or oven, and is then re-rolled once annealed or sintered.
Since it is not as harsh on the woven wire, the continuous process will be a better fit if you are working with finer mesh specifications or you need a roll width that is 24” or less.
When Should I Anneal My Wire Mesh?
As stated above, annealing makes woven wire easier to manipulate. That being said, the annealing process is used when a project calls for the mesh to be configured into a customized form.
Annealing your mesh will ensure that the wires retain this shape. In most cases, it's all that's needed when forming woven wire.
A great example of annealed woven wire in use can be seen in molded pulp manufacturing facilities. These facilities form annealed mesh into custom moldings in order to create various containers, such as egg cartons.
Read the following article for a full breakdown of what the annealing heat treatment process consists of:
When Should I Sinter My Wire Mesh?
Sintering is typically used to prevent the wires within the mesh weave from moving or falling out over time. It is perfect for filtration applications, such as oil filtration, that rely on the retention of the mesh pore size to filter out unwanted debris.
Sintering is also an ideal solution for bonding multiple layers together, as seen in our Porostar® filters, and multiple layers of mesh to a perforated plate. It can also be used to bond a single layer of mesh to perforated plate as well.
To get a better understanding of how sintering various wire mesh layer configurations can benefit your process, read the article linked below:
What Are the Disadvantages of Sintering or Annealing Your Wire Mesh?
Naturally, there are additional processing times and expenses associated with both heat treatment methods.
So, for example, if you order a roll of woven wire that is neither sintered or annealed, you would have the roll at your facility in about a week and only pay the cost of the roll.
On the other hand, if you take that same roll of wire mesh and either sinter or anneal it, you would have to cover the cost of the roll as well as the additional costs of the heat treatment process. The time frame for delivery would also be extended by a few weeks.
Learn More About Forming Wire Mesh
In order to provide wire mesh solutions that are tailored to the needs of the customer, an annealing or sintering heat treatment process is often applied.
Annealing is the heat treatment process used to reduce the internal stress and hardness of the individual wires of the mesh weave. This, in turn, makes the woven wire easier to work with and ensures the wires do not flex back to their original profile.
Sintering is the heat treatment process in which the woven wire is heated to just below its melting point, causing the individual wires to bond at each intersection. This method is used to preserve the pore size of the woven wire by preventing the wires within the weave from moving.
As both heat treatment processes are used to preserve the performance of wire mesh when formed, it's critical that you understand what can and cannot be done during the forming process. This will help you implement wire mesh solutions that produce results for a prolonged period of time.
W.S. Tyler has been in the wire weaving business for over 150 years and is here to help you understand the possibilities of woven wire mesh.
To gain insight into how you can form wire mesh to fit a specific application, refer to the article below:
About Ronnie Brown
Ronnie is the Content Writer for W.S. Tyler and has four years of experience as a professional writer. He strives to expand his knowledge on all things particle analysis and woven wire mesh to leverage his exceptional writing and graphic design skills, creating a one-of-a-kind experience for customers.