Screen Printing Printed Circuit Boards: The Impact of Woven Wire Mesh
Screen printing has been used for centuries for things such as advertising posters to product labeling. Despite having been around for so long, the fundamentals of the process have remained unchanged.
As the digital era we live in continues to introduce technology that is integrating itself into how traditional things were done, you’d think screen printing would be a dying industry. Well, the fact of the matter is that it's more important than ever, as screen printing plays an integral role in the manufacturing of the circuit boards that power this technology.
With woven wire standing as a prominent screening medium, W.S. Tyler feels responsible for educating customers on how woven wire can be applied to their process and how it stacks up against other materials.
And for this reason, we wrote the following article to provide insight into the role woven wire mesh has during the manufacturing of printed circuit boards by covering:
- What screen printing is
- What woven wire mesh is
- How woven wire influences the production of printed circuit boards
- Why you should be considering incorporating woven wire mesh
What Is Screen Printing?
Screen printing is the process in which a screening medium, such as silk, polyester, nylon, plastic, or woven wire mesh, is used to transfer a pattern onto a surface with ink. A special epoxy is applied to the screen to ensure ink is blocked off in accordance to the design, essentially creating a stencil.
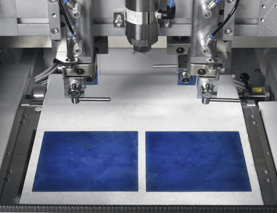
Now, ink transfer is carried out in one of five ways: the flatbed method, the stationary cylinder method, the cylinder method, the cylindrical textile method, and the roll-to-roll method. Regardless of what method you use, the idea behind the process is, for the most part, the same.
What is meant by this is that the basic concept of screen printing involves flooding the screening media until the unblocked pore openings are filled with ink. A squeegee-like mechanism is then used to press the screen onto the surface while simultaneously distributing the ink, making sure the design is transferred evenly in its entirety.
Get to know the five most widely used screen printing techniques in the
article below:
What Is Woven Wire Mesh?
Woven wire mesh is best defined as hundreds of metallic wires interlocked in both the vertical and horizontal direction after a centuries-old weaving technique is applied. When implementing wire mesh for screen printing applications, parameters including the wire diameter, mesh count, aperture size, thickness, width, and length are predetermined before being woven.
Additionally, post-weaving value-added services can be applied to improve the characteristics of the mesh to ensure the mesh best accommodates your operation.
How Does Screen Printing Affect Printed Circuit Board Production?
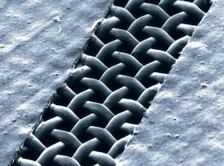
Printed circuit boards, or PCBs, are conductive boards designed to relay electrical currents to several electrical components, such as semiconductors, to execute a derided function. They are most commonly used to control electronic devices like computers and smartphones.
To ensure effective circuits, printed circuit boards often start as a sheet of copper as the alloy is known for its conductivity. An engineer will design and layout how the circuits should connect, which are etched onto the copper, forming copper traces.
To prevent oxidation and potential faults, a solder mask is applied, leaving only the copper traces exposed. This solder mask is what gives circuit boards their iconic green color and is applied via screen printing.
Additionally, screen printing is often employed during the final production stages, where the components sections and other labelings are marked for the end-user.
Why Use Woven Wire Mesh?
There are a number of reasons why you want to use woven wire mesh when screen printing printed circuit boards. Compared to other screening media, wire mesh delivers a heightened level of tensioning capabilities, durability, heat resistance, and precision.
Taking a closer look, materials, such as nylon and polyester, have a 5% elongation, whereas woven wire mesh has below 1%. W.S. Tyler, in particular, conducts several integrity tests to calculate the exact amount of tension the mesh can withstand before breaking.
Now, because wire mesh is far more durable than other materials, it can withstand greater tension loads. This can be critical when finer mesh counts are needed to depict more detailed designs.
The Importance of Calendaring
With any screen media, friction between the knuckles of the screen intersections and the squeegee is one of the more notable concerns. This is because this friction increases the possibility of encountering subtle yet noticeable inconsistencies in the prints.
Fortunately, wire mesh can be calendared. Calendaring is the process in which the mesh is run between two rollers and endures tremendous amounts of simultaneous heat and pressure. As a result, the knuckles of the mesh are flattened, and the overall thickness of the mesh is reduced.
This makes for a smoother surface which reduces the friction, making for more consistent prints and extending the lifespan of your squeegee.
Accurate Screen Printing Starts With the Right Mesh Count
Printed circuit board manufacturers often turn to woven wire mesh as a screen-printing apparatus to create masks that only expose desired points of the circuit that run throughout the board. This is because woven wire mesh delivers the customization and post weaving options needed to accurately protect the board from oxidation and shorts.
But regardless of what screen printing process you use, the mesh count of the screen is possibly the most critical specification to calculate. This is because the mesh count ultimately controls the efficiency of the ink distribution.
W.S. Tyler has over 140 years of experience manufacturing woven wire mesh and wants to use the knowledge gained over the years to help screen printers find the mesh counts that accurately depict the desired design or mask.
With that, the following article will serve as a guide to help you through the process of determining what mesh count you should use to distribute your ink designs:
About Ronnie Brown
Ronnie is the Content Writer for W.S. Tyler and has four years of experience as a professional writer. He strives to expand his knowledge on all things particle analysis and woven wire mesh to leverage his exceptional writing and graphic design skills, creating a one-of-a-kind experience for customers.